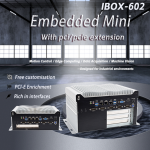
Date: 19 July 2024
PLC automation control is mainly manifested in the input and output of IO, input and output of analog sensors, pulse or bus-type motion control. HMI is used to display process data, status information and operation interface, and operators can interact with the automation system through the HMI to monitor, adjust and control operations. Traditional PLC program is difficult to cope with complex industrial application scenarios, such as the need to interface with the MES or other production management systems, enterprises are generally through the addition of host computer (industrial computer) to meet the application expansion. Adding a host computer is usually accompanied by the use of an industrial monitor, or directly use the industrial all-in-one machine.
Limited computational power PLCs:
PLCs have relatively limited processing power and may not be able to meet the demands of complex algorithms and large data processing. This may limit the intelligence and optimization capabilities of the system.
Lack of Flexibility:
PLCs are often programmed using specific programming languages and hardware architectures, which makes it relatively difficult to modify and expand the system. PLCs may not be flexible enough for applications that require frequent changes or customization.
Weak communication capabilities:
Traditional PLCs may have limitations in communicating with other devices and systems. This hinders system integration and data sharing, affecting overall productivity and informationization.
Complex Programming and Debugging:
PLC programming requires professional knowledge and experience, for some complex control logic, programming and debugging will be more cumbersome and time-consuming, at the same time, a lot of PLC debugging needs to be used to program, compared to the X86 program seems to be more complex.
Limitations on Data Analysis:
PLCs usually PLCs usually provide limited visualization interfaces and data analysis functions, which makes it difficult for operators to gain a deeper understanding of the system’s operating status and make effective decision support.
Equipment costs:
If the enterprise equipment itself is not very profitable, in the existing PLC + touch screen on the basis of increasing the industrial control machine, will certainly make the enterprise equipment procurement costs significantly higher. But because of the system design needs, and have to use PLC + touch screen + industrial control machine.
Personnel costs:
Increase the host computer, means that the system software to do re-development, if the enterprise’s current PLC technicians do not know much about the industrial control machine, then you may also need to be equipped with an additional technician who knows how to program the industrial control machine, which undoubtedly increases the cost of employing the enterprise.
Maintenance costs:
the simultaneous use of PLC + industrial control machine, means that there are two systems, the need for both sides of the technical staff docking, in the project development cycle will significantly increase the time, if a node failure, but also need to troubleshoot the two together, to the enterprise to increase the high cost of maintenance.
Hardware Selection:
Select the industrial computer with high performance processor, large capacity memory and storage to meet the control requirements of the equipment, at the same time, according to the interface requirements of the equipment, select the appropriate input and output modules and communication modules.
Operating system selection:
choose a stable and reliable industrial-grade operating system, such as Windows 10 IoT Enterprise or Linux, these operating systems have better real-time and stability, and can meet the requirements of industrial control.
Software development:
Use the appropriate programming software, such as C++, C# or Python, to develop the control program of the device, these programming languages have higher flexibility and expandability, and can realize more complex control logic and algorithms.
Data Acquisition and Monitoring: Through the Ethernet interface or other communication interfaces of the industrial control machine, realize the communication with the equipment and data acquisition. At the same time, the use of configuration software or self-developed monitoring interface to achieve real-time monitoring of equipment and data display.
System integration:
Integrate the industrial control machine with other components of the equipment, including sensors, actuators, motors, etc., to ensure that the communication and coordination between the various components work properly.
Higher performance:
Industrial controllers have stronger computing power and data processing capability, which can realize more complex control algorithms and logic and improve the performance and accuracy of the equipment.
Better expandability:
Industrial controllers have rich interfaces and slots, which can easily expand functions and connect external devices to meet different application requirements.
Easy to maintain and upgrade:
The hardware and software of industrial controllers are relatively more common, and can be easily maintained and upgraded, reducing maintenance costs and cycles.
Improve productivity:
Through the use of industrial controllers, you can realize more efficient production process control and management, improve production efficiency and quality.
Cost-effective and simplified system integration:
Reduced hardware costs for PLCs and configuration screens, as well as reduced hardware and development and maintenance costs, reduced device count and complexity, and reduced maintenance and troubleshooting difficulties.
Integrated data acquisition and monitoring:
Integrate the IPC with other components of the device, including sensors, actuators, and motors, and realize communication and data acquisition with the device through the rich ports of the IPC.
Data Acquisition and Analysis:
Enables easier acquisition and analysis of production data for real-time monitoring, quality control and production optimization.
Advanced functions and easy programming and development:
With more powerful data processing capabilities, remote monitoring and intelligent control functions, using more modern programming tools and development environment, improving the development efficiency.
Reliability and stability:
Tuolang industrial control equipment has undergone rigorous market application polishing and has a leading advantage in the field of industrial automation control.
Real time requirements:
We have optimized the system for industrial automation scenarios to meet the real-time requirements of 95% of industrial applications in the market.
Electromagnetic compatibility:
The product has passed EMC electronic compatibility certification, meets the requirements of anti electromagnetic interference, has good electromagnetic compatibility, and is free from electromagnetic interference.
Security:
For certain scenarios designed for industrial application security, we have customized embedded systems to meet the safety requirements of project sites.
Date: 19 October 2024
TPIPC: Deeply committed to industrial computers, micro-innovation to help customers grow.
Introduction: In VisionChina2024 (Shenzhen) on October 14-16, the organizer, Machine Vision Industry Union (CMVU), had the honor to have an in-depth communication with Mr. Dong Huying, the general manager of Dongguan Tuolang Industrial Equipment Co. In this interview, Mr Dong not only shared the development history and core competitiveness of Tuolang Industrial Equipment Co, but also introduced in detail the company’s innovations and future plans in the field of machine vision. Through Mr Dong’s speech, we can deeply understand how Tuolang Industrial Equipment Co maintains steady growth in the fierce market competition and actively expands overseas market by virtue of micro-innovation and precise market positioning.
Reporter: Hello, Mr Dong! I am very glad to have a chance to communicate with you. First of all, could you please give us a brief introduction to Tuolang Industrial Equipment Co?
Mr Dong: Hello, I am Mr Dong from Tuolang Industrial Equipment Co. Founded in 2016, Tuolang Industrial Equipment Co is a national high-tech enterprise and a speciality enterprise in Guangdong Province. We have been committed to the development and manufacture of industrial computers, providing highly reliable and high-level industrial PC-based control solutions for various segments of the industry. The main production and management products are: embedded industrial controllers, desktop wall-mounted industrial controllers, rack-mounted industrial controllers, industrial all-in-one PCs, industrial monitors and other series of products. Our products in all kinds of large-scale projects have been verified, in industrial automation, energy and power, machine vision, edge computing, deep learning, motion control and other industries have received high standards of customer evaluation. In my opinion, vision plus industrial controller undoubtedly plays the core role of ‘eyes’ and ‘brain’ of the equipment in the field of vision, so we attach great importance to both, thanks to the company always adhere to the principle of quality first, continue to increase investment in research and development, and provide accurate solutions for the The company has always insisted on the principle of quality first, continued to increase investment in R & D, and provide accurate solutions for the industry segments. Because of this, the company has been able to maintain a steady growth of more than 30% per year.
Reporter: In VisionChina2024 (Shenzhen), what are the highlights of Tuolang Industrial Equipment Co products? What are the outstanding performances of these products in practical applications? Can you share with us?
Mr Dong: Sure, very happy to share. In the current vision field, we clearly feel the increasing competition in the low-end market, while at the same time, there is a growing demand for 3D vision. This trend puts higher demands on the computers’ arithmetic power and performance. To meet this challenge, we at Tuolang Industrial Equipment Co have launched a fanless industrial computer with 12th and 14th generation Intel desktop processors. This product supports discrete graphics cards such as 4060, and is equipped with 10 network ports, each of which can provide a 2.5G connection rate while supporting up to two GPUs, thus dramatically increasing the arithmetic power and performance of machine vision, and greatly improving the productivity of the equipment.Reporters:How do you think differences in arithmetic and performance will distinguish the vision industry from other industries?
Mr Dong: Machine vision has a wide range of applications, but I think the market is currently experiencing increasing demand for highly reflective, highly detailed, and 3D vision. Because these applications have high resolution and involve 3D depth detection, they require extremely high GPU arithmetic. Therefore, we usually first determine the usage scenarios with our customers and then make recommendations for performance requirements. This is significantly different from our general industrial control needs, and, while some applications have common needs, they have high rate requirements and require multiple cameras to be connected. As an industrial computer provider, we need to provide superb performance to enable a machine to connect more cameras, e.g. from 4 to 10 or even 15, and process 60 frames per second. In this way, customers can reduce application costs and overall solution costs.
Reporter: The machine vision industry is a dynamic field of scientific and technological innovation, what do you think are the core characteristics of an innovative enterprise? How does your company continue to promote and maintain this innovative ability?
Mr Dong: In my opinion, the innovation ability of an enterprise is firstly based on a deep insight into the market. Innovation must be able to solve the shortcomings of existing products or services in the market and create real value for customers, so that customers are willing to pay for innovation. Personally, I like this industry very much. The application of industrial controllers as computing terminals involves numerous subsectors, which provide us with rich and diverse needs. After grasping the needs of our customers, we will gain an in-depth understanding of their application scenarios and, relying on our professional strengths, provide them with more micro-innovations in terms of integration and optimisation. For SMEs, I think micro-innovation can more directly help customers save the cost of use, simplify the programme, and make the innovation more grounded and practical. Therefore, we have been committed to integrating applications in niche industries based on industrial controllers to provide valuable and groundable micro-innovation solutions to help customers reduce costs and increase efficiency. In this way, we continue to drive and maintain the innovation capability of our business, ensuring that we continue to move forward in the dynamic industry of machine vision. In my field of vision, for example, vision used to be separate from light sources and industrial controllers. We have responded to the needs of our customers with a wide range of circuits by integrating the light source inside the industrial controller, which can be seen as a micro-innovation. Another thing we are currently working on is that motion control is often involved in vision systems. The traditional solution is either to insert a motion control card, which tends to cause vibration problems, or to separate the motion control and handle it with another industrial control machine, which in turn leads to communication real-time problems. What we are doing now is to highly integrate vision, light source and motion control, and at the same time reduce the size so that customers can have more flexibility in their wiring solutions and applications. I think this is also a very practical micro-innovation. Whether it’s from the perspective of cost, programme or cost reduction and efficiency, innovation only has value if it really improves the productivity efficiency of the customer.
Reporter: What are your unique views and plans for overseas markets and their layout?
Mr Dong: Actually, for the overseas market, I always think it will become an important direction for our company’s future development. In the past, the centre of the international market of the industrial control machine industry might be in Taiwan and Germany. Since Tuolang Industrial Equipment Co has been involved in foreign trade since 2020, I obviously feel that the domestic growth rate in the past two years has been very fast, and the relevant industrial chain of China has demonstrated a strong competitiveness in the international market, which is expected to become the centre point of this industry in the future. Specifically, what we can complete in a week may take two or three months or even longer abroad to achieve the same efficiency. In addition, the industrial chain of our entire industry has become quite mature, and the trend of transferring to overseas is becoming more and more obvious.
Reporter: In these two years, what are the specific plans of Tuolang in the sea? What is the proportion of foreign trade in Tuolang’s business?
Mr Dong: The proportion of our foreign trade is growing very fast, and we have established long-term cooperation with some head enterprises in Europe. Their orders are obviously much larger than domestic orders. For us, the vision must be broadened, not just limited to the domestic market. Overseas markets not only have great potential, but also help us improve product quality and internationalisation. Therefore, we will continue to increase the expansion of overseas markets and seek more opportunities for cooperation.
Reporter: At VisionChina 2024 in Shenzhen, the concept of ‘Vision plus x’ was proposed, aiming to explore the new boundaries of machine vision. What’s your insight on this concept?
Mr Dong: I think vision plus AI is the core of ‘Vision plus x’. From the device level, devices are now getting smarter and smarter with the addition of AI processing, especially deep AI, which enables them to work more proactively. In fact, many cutting-edge concepts, such as humanoid robots or digital people, will ultimately rely on the expanded application of vision and AI in order to realise on-the-ground applications. Therefore, I believe the future market opportunities in this area will be very large.
Reporter: What is your overall impression of this VisionChina2024 Shenzhen exhibition?
Mr Dong: My overall impression of this exhibition is quite good. There were really a lot of impressive exhibits of cross-border convergence technologies, demonstrating the wide range of applications and potential of machine vision in various fields. The exhibition halls were well patronised and the progress in the field of machine vision was particularly remarkable, clearly showing a shift from traditional 2D to 3D, a change that impressed me and made me look forward to the future of machine vision.
In addition, I can clearly feel that in the whole industrial chain, our domestic manufacturers cooperate quite well with each other. They were able to quickly bring many high-precision projects to fruition, and this efficient collaboration is remarkable.
Reporter: Please share what development plan Tuolang Industrial Equipment Co has in 2025?
Mr Dong: Looking ahead, I think the combination of 3D+AI and vision technologies will be an important trend in the future. These technologies will bring a wider range of application scenarios and higher precision to machine vision, which will drive the further development of the industry.Tuolang Industrial Equipment Co will continue to follow the industry trend in 2025, and increase the R&D investment in the combination of 3D+AI and vision technologies. We hope to bring more advanced and reliable machine vision solutions to the market through continuous innovation to meet the growing needs of our customers.
Date: 12 August 2024
As we all know, small mini class of industrial controllers due to the size and board adaptation requirements, most of the choice of low-voltage specifications processor, its low power consumption, small size and other advantages, such as the office class of ultra-thin book, business book, but in terms of performance and conventional desktop PC processors still have a certain performance gap. Both to meet the CPU performance and to meet the appearance of small size, in order to address this market demand, Tuolang Industrial Equipment Co self-research based on the standard voltage processor mini fanless industrial computer, the following to understand.
There are several main reasons for using low-voltage processors in small machines:
Power Consumption Control: Low voltage processors typically have lower power consumption, which helps to reduce the overall power consumption of a small form factor machine and reduces the need for heat dissipation, thus allowing the device to dissipate heat more efficiently in a smaller space and maintain a stable operating temperature.
Energy efficiency and range: For some mobile or portable small form factor devices, energy-efficient features are important to extend battery life, allowing them to operate for longer periods of time without external power.
Thermal design: Due to the limited size of a small form factor, a low-power, low-voltage processor generates less heat, simplifying the design of the cooling system and helping to reduce the size and weight of the device.
Cost control: Low voltage processors are usually relatively low in cost, helping to reduce the overall production cost of small form factor PCs and making them more competitively priced.
Meeting basic performance needs: For some specific application scenarios, such as simple data processing, file storage and light office work, the performance of low-voltage processors is sufficient to meet the needs without the need for higher performance but also higher power consumption of standard voltage processors.
Tuolang Industrial Equipment Co self-developed IBOX-602 series, the whole system adopts desktop-level standard pressure processor. In order to meet the performance at the same time, through years of technical experience, the use of the body of aluminium alloy + copper self-conducting thermal technology, successfully achieved the whole machine fanless cooling, effectively reducing the noise interference with the technical indicators. Built-in expansion is the industry’s leading, the maximum support for 3-way PCI/PCIE card slot board, almost covering the majority of computer peripherals. Integrated digital capacitor isolation module + TVS protection, with surge protection, high-speed transmission at the same time the data does not fall out of the frame, but also to protect the back of the circuit components are not due to transient high-voltage impact and damage.
The advantages of using standard-voltage processors for small-size industrial control machines are mainly reflected in the following aspects:
Good performance: compared with low-voltage processors, the performance of standard voltage processors is stronger, which can better meet the higher requirements for computing power in industrial control.
Feature-rich: able to support multiple operating systems, can be customised according to the needs of the configuration, and has a wealth of interfaces to meet the diverse expansion needs.
Adapt to complex tasks: can effectively respond to more complex multi-tasking system, to ensure the stable operation of the system. Standard pressure processor can carry out real-time online detection and control of industrial production processes, give a quick response to changes in working conditions, timely collection and output adjustment.
However, the standard pressure processor power consumption is relatively high, the general TDP (thermal design power consumption) in the 35W to 45W between or even higher, if the battery power supply time is relatively short. But for small-sized industrial controllers, in some specific industrial scenarios, more important is its performance and functionality, negligible requirements for battery life.
At the same time, small-sized industrial controllers themselves have the advantages of small size, space-saving, easy to install and so on. For example, it can be placed in any corner of the desktop at will, or fixed behind the monitor or TV screen with a special bracket, and some products also support a variety of installation methods such as rail mounting and wall mounting.
In practice, the choice of standard-voltage processor or low-voltage processor small size industrial control machine, need to take into account the specific industrial application scenarios, the performance and endurance requirements and other factors. If the industrial control task is more complex, the computing power requirements are higher, and there is a certain limitation on the size of the device, then the use of standard-voltage processors of small-sized industrial controllers may be a more appropriate choice.
Date: 20 August 2024
This paper discusses in detail the important role and application methods of industrial controllers in the transformation of manufacturing industrial control equipment. By analysing its advantages in data processing, real-time control, stability, etc., it explains how to use industrial controllers to improve the efficiency and quality of industrial production. The text lists the actual cases in which Tuolang is involved, and looks forward to the future development trend, providing a useful reference for the technological upgrading of related fields.
In today’s highly automated industrial production environment, the performance and efficiency of industrial control equipment is crucial to the competitiveness of enterprises. With the continuous progress of science and technology, artificial intelligence scenes all over the street, the traditional industrial control equipment is gradually difficult to meet the growing demand for production and the current trend of energy saving and environmental protection, its transformation and upgrading has become an inevitable choice. As a high-performance, highly reliable industrial control computer, industrial control equipment in the transformation and upgrading plays a key role in improving industrial production efficiency has brought new opportunities.
The characteristics and advantages of industrial control machine:
(1) Powerful data processing capability
Equipped with a high-performance processor and high-capacity memory, industrial controllers are able to stably run business software and quickly process a large amount of industrial data, realise complex algorithms and model calculations, and provide powerful support for precise control and optimised production.
(2) Real-time control performance
With high-precision real-time clock, fast interruption response and self-recovery capability, it can ensure real-time monitoring and control of industrial processes, handle various emergencies in a timely manner, and reduce production delays and losses.
(3) Stability and reliability
Adopting industrial-grade hardware components and professional design, it is able to operate stably for a long time in harsh industrial environments, with strong anti-jamming ability, and adapt to harsh environmental conditions such as high temperature, high humidity and vibration. (D) Rich interfaces and expandability
With a variety of interfaces, such as RS232/485 serial port, Gigabit / 10 Gigabit network port, USB port, PCI expansion slot, etc., it is easy to connect and communicate with a variety of industrial equipment. At the same time, it has good expandability, and hardware modules can be added flexibly according to actual needs to meet different functional requirements.
Application areas of industrial control machine in the transformation of industrial control equipment
(1) Manufacturing automated production line transformation
In automated production lines such as automobile manufacturing, electronic equipment production, etc., industrial controllers can be used to control robots, conveying equipment, processing machine tools, etc., to achieve automation and intelligence of the production process and improve production efficiency and product quality.
(2) Energy industry equipment monitoring and optimisation
In the field of electric power, oil, natural gas and other energy, industrial control machine can be used to monitor the operation status of power generation equipment, power transmission and transformation equipment, oil and gas extraction equipment, data analysis and fault diagnosis, to achieve optimal operation and preventive maintenance of equipment.
(3) Intelligent transport system in the transport industry
In the field of railway, highway, aviation and other transport, industrial control machine can be used to control signal lamps, charging system, vehicle detection equipment, etc., to achieve intelligent regulation of traffic flow and safety management.
(4) Environmental monitoring and management equipment
It is used in air quality monitoring and water quality monitoring equipment of environmental monitoring stations, as well as the control system of sewage treatment plants and waste gas treatment equipment, to realise real-time collection and processing of environmental data, and to safeguard the effect of environmental governance.
Specific implementation of industrial controllers in the transformation of industrial control equipment:
(1) System integration
Integrate the industrial control machine with existing sensors, actuators, controllers and other equipment to build a complete industrial control system. By writing control programs and algorithms, it achieves precise control and optimisation of the production process.
(2) Data acquisition and analysis
Using the high-speed data acquisition interface of the industrial controller, various data during the operation of industrial equipment are collected, such as temperature, pressure, flow, speed, etc.. These data are processed and mined through data analysis software to extract valuable information, which provides the basis for equipment maintenance and process improvement.
(3) Remote monitoring and diagnosis
With the help of network communication technology, the industrial control machine is connected to the internal network or the Internet to achieve remote monitoring and diagnosis of industrial equipment. Technicians can view the real-time running status of the equipment at the remote terminal, find and solve problems in time, and reduce equipment downtime.
(4) Human-computer interaction interface design
Develop a friendly human-computer interaction interface so that operators can conveniently operate and monitor industrial equipment. Through graphical display, touch operation and other ways to improve the convenience and accuracy of operation.Practical case studies
(1) A parts production company’s automated production line transformation
The original production line of the enterprise adopts traditional PLC control, low production efficiency and unstable product quality. Through the introduction of industrial control machine, the production line has been comprehensively transformed. The ICP controls multiple robots to carry out precise material handling and assembly, and at the same time collects and analyses data in real time during the production process to optimize the production process. After the transformation, the production efficiency of the production line has increased by 35%, and the qualification rate of the products has increased to more than 99%.
(2) Equipment Monitoring and Optimisation System for a Wind Farm
The equipment of the wind farm is widely distributed, operating in a harsh environment and difficult to maintain. A set of equipment monitoring and optimisation system is constructed by using an industrial computer to monitor the running status, wind speed, wind direction and other parameters of the wind turbine in real time. Through data analysis and intelligent algorithms, the maximum power tracking and preventive maintenance of the wind turbine is achieved, which improves power generation efficiency and reduces maintenance costs.
Challenges and Solutions
(1) Complexity of the industrial environment
There are many unfavourable factors such as electromagnetic interference, vibration, dust, etc. in industrial sites, which may affect the normal operation of industrial controllers. Solutions include the use of anti-interference hardware design, sealing protection measures, heat dissipation optimisation, etc.
(2) System compatibility issues
When integrating with old equipment, compatibility problems such as mismatched interfaces and inconsistent communication protocols may be encountered. This is solved by using conversion modules, developing middleware, etc.
(3) Network security threats
With the development of the industrial Internet, industrial controllers face the risk of network attacks. Security measures such as network isolation, encrypted communication, and identity authentication are taken to ensure the safe operation of the system.
Future Development Trends
(1) Intelligent
Integration of artificial intelligence, machine learning and other technologies, so that the industrial control machine with more powerful intelligent control and decision-making capabilities, to further improve production efficiency and quality.
(2) Edge computing
With the popularity of the Industrial Internet of Things, industrial controllers will take on more of the tasks of edge computing to achieve local processing of data and real-time response, reducing data transmission delays and network bandwidth pressure.
(3) Openness and interoperability
Support more open standards and protocols, improve interoperability with equipment from different manufacturers, and promote the integration and collaborative work of industrial control systems.
Conclusion:
The application of industrial controllers in the transformation of industrial control equipment has brought significant efficiency gains and quality improvements to industrial production. By giving full play to its powerful data processing capabilities, real-time control performance, stability and scalability, it can achieve automation, intelligence and optimised operation of industrial production. However, in practical applications, it still needs to face various challenges and continuously explore innovative solutions. With the continuous development of technology, industrial controllers will play a more important role in the industrial field, promoting industrial production to a higher level.
As we all know, small min
TPIPC: Deeply committed t